H2S Monitor Calibration: Essential Guide for Safety and Efficiency
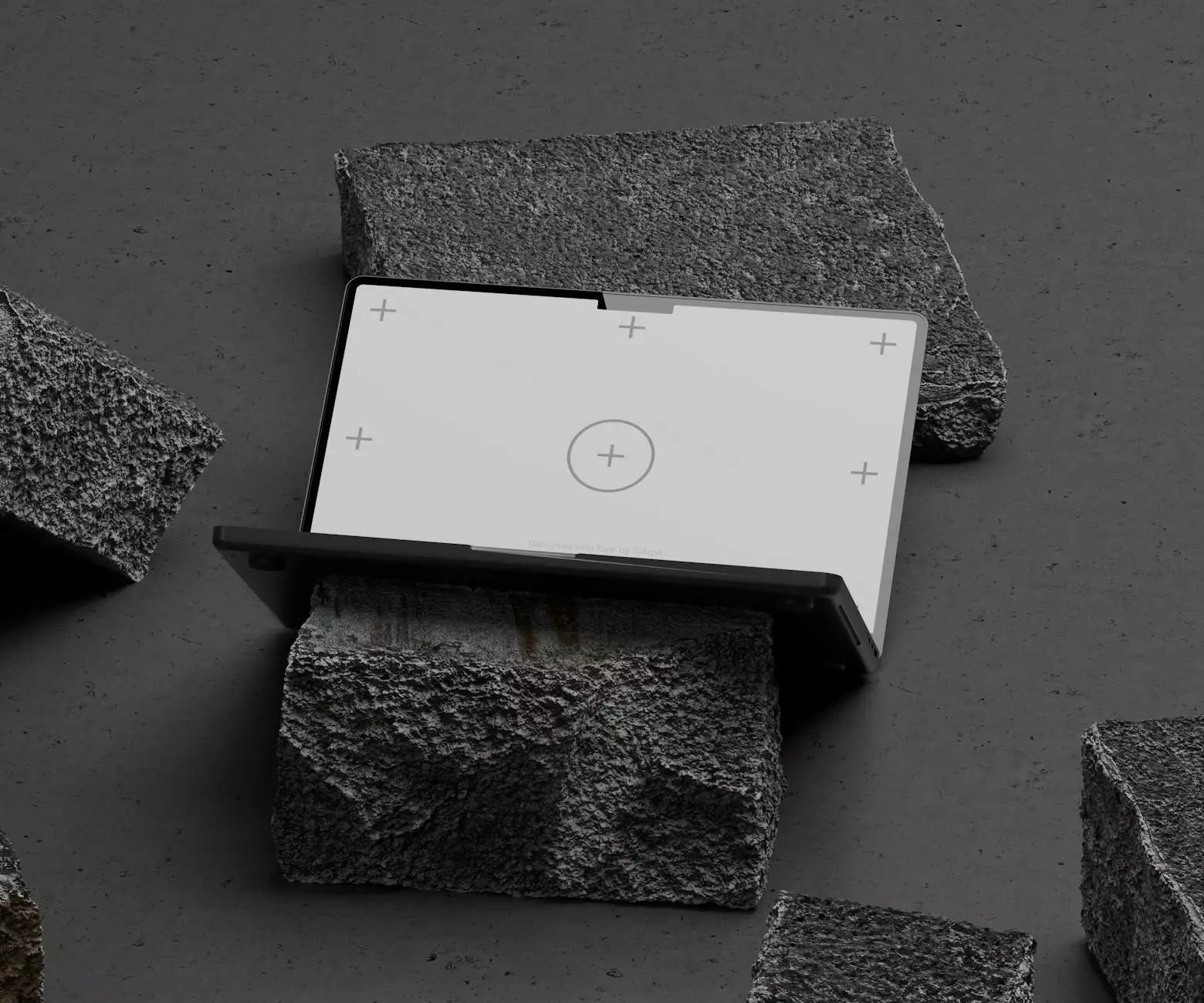
Hydrogen sulfide (H2S) is a colorless gas known for its foul odor, resembling that of rotten eggs. It poses serious health risks to employees in various industries, particularly in sectors such as oil and gas, mining, and waste treatment. To ensure a safe working environment, regular H2S monitor calibration is critical. This guide will delve into its importance, methods, benefits, and best practices crucial for maintaining effective monitoring systems.
Understanding H2S Monitoring
Monitoring H2S levels in the workplace is a vital component of occupational health and safety. An effective H2S detection system allows for:
- Early detection of harmful gas concentrations.
- Prevention of potential health risks.
- Compliance with regulatory standards.
To maximize the effectiveness of these monitoring systems, regular H2S monitor calibration is necessary.
What is H2S Monitor Calibration?
H2S monitor calibration refers to the adjustment of H2S detectors to ensure accurate readings. Calibration is performed to align the instrument’s response to known concentrations of H2S gas, confirming that it can detect even low levels of the gas effectively.
The Importance of H2S Monitor Calibration
Regular calibration is essential for various reasons:
- Accuracy: Over time, sensors can drift, leading to inaccurate measurements. Calibration ensures that readings are precise, enabling timely responses to dangerous levels of H2S.
- Regulatory Compliance: Many industries are subject to strict regulations that mandate regular calibration of monitoring equipment, enhancing workplace safety and minimizing liabilities.
- Equipment Lifespan: Regular maintenance, including calibration, contributes to the extended lifespan of monitoring equipment, saving costs associated with premature replacements.
- Worker Safety: Above all, accurate readings from H2S monitors can prevent accidents and protect the health of workers exposed to high-concentration environments.
Calibration Procedures for H2S Monitors
The calibration process differs depending on the specific type of H2S monitor used, but generally, it involves the following steps:
1. Prepare the Calibration Equipment
Gather all necessary tools and equipment, including:
- Calibrated gas cylinders with known concentrations of H2S.
- Calibration gas flow regulator.
- Appropriate personal protective equipment (PPE).
- Calibration software (if applicable).
2. Set Up the Monitoring Device
Ensure the monitoring device is powered on and set to the correct mode for calibration. Refer to the manufacturer's manual for specific instructions related to your equipment.
3. Introduce Calibration Gas
Using the flow regulator, introduce the calibrated H2S gas to the monitor. This should be done slowly to avoid overwhelming the sensor.
4. Adjust the Monitor
Once the gas is introduced, check the readings on the monitor. Adjust the device using the calibration controls until the monitor displays the expected concentration level. Some monitors might require a software update or settings adjustments.
5. Confirm Calibration
After adjustments, it’s important to confirm that the device accurately reflects the known concentration of H2S. Test with multiple concentrations to ensure reliability.
6. Document the Calibration
Finally, record the calibration results, including the date, technician's name, equipment details, and any adjustments made. This documentation provides evidence of compliance with regulatory standards.
Frequency of H2S Monitor Calibration
The frequency of H2S monitor calibration can depend on several factors, including:
- Manufacturer recommendations.
- Frequency of use — systems used in high-risk environments may require more frequent calibration.
- Environmental conditions such as temperature and humidity.
Typically, it is advisable to calibrate gas detectors at least once a month, but always refer to the manufacturer’s guidelines.
Best Practices for H2S Monitor Calibration
To ensure effective calibration and maintenance of H2S monitors, consider adopting the following best practices:
- Establish a Calibration Schedule: Develop a routine calibration schedule and stick to it to ensure all devices are consistently calibrated.
- Train Personnel: Ensure that employees performing calibrations are adequately trained and understand the processes involved.
- Use Quality Calibration Gases: Always use certified calibration gases from reputable suppliers to avoid inaccurate readings.
- Regularly Inspect Equipment: Conduct visual inspections of the monitors to identify signs of damage or wear and tear.
- Maintain a Calibration Log: Keeping a detailed log of all calibration activities can help in compliance audits and provide accountability.
Advantages of H2S Monitor Calibration
The advantages of regular and efficient H2S monitor calibration extend beyond compliance and accuracy:
- Increases overall workplace safety.
- Encourages a culture of safety among employees.
- Facilitates quick responses to potential risks.
- Reduces the likelihood of costly accidents and incidents.
Conclusion
In conclusion, the significance of H2S monitor calibration cannot be overstated. It is a fundamental practice that ensures the safety of workers in industries where hydrogen sulfide exposure is a risk. Regular calibration helps maintain the accuracy of H2S monitors, thereby protecting employees and fostering a safer work environment. Organizations such as H2S Online Training provide resources and training for effective monitoring and calibration practices, ensuring compliance and maintenance of operational safety standards.
Investing in proper H2S monitor calibration and ensuring adherence to best practices not only protects your workforce but also contributes to the overall efficiency and reliability of the operations that rely on these essential safety instruments.