Understanding Tube Connection Types: A Comprehensive Guide
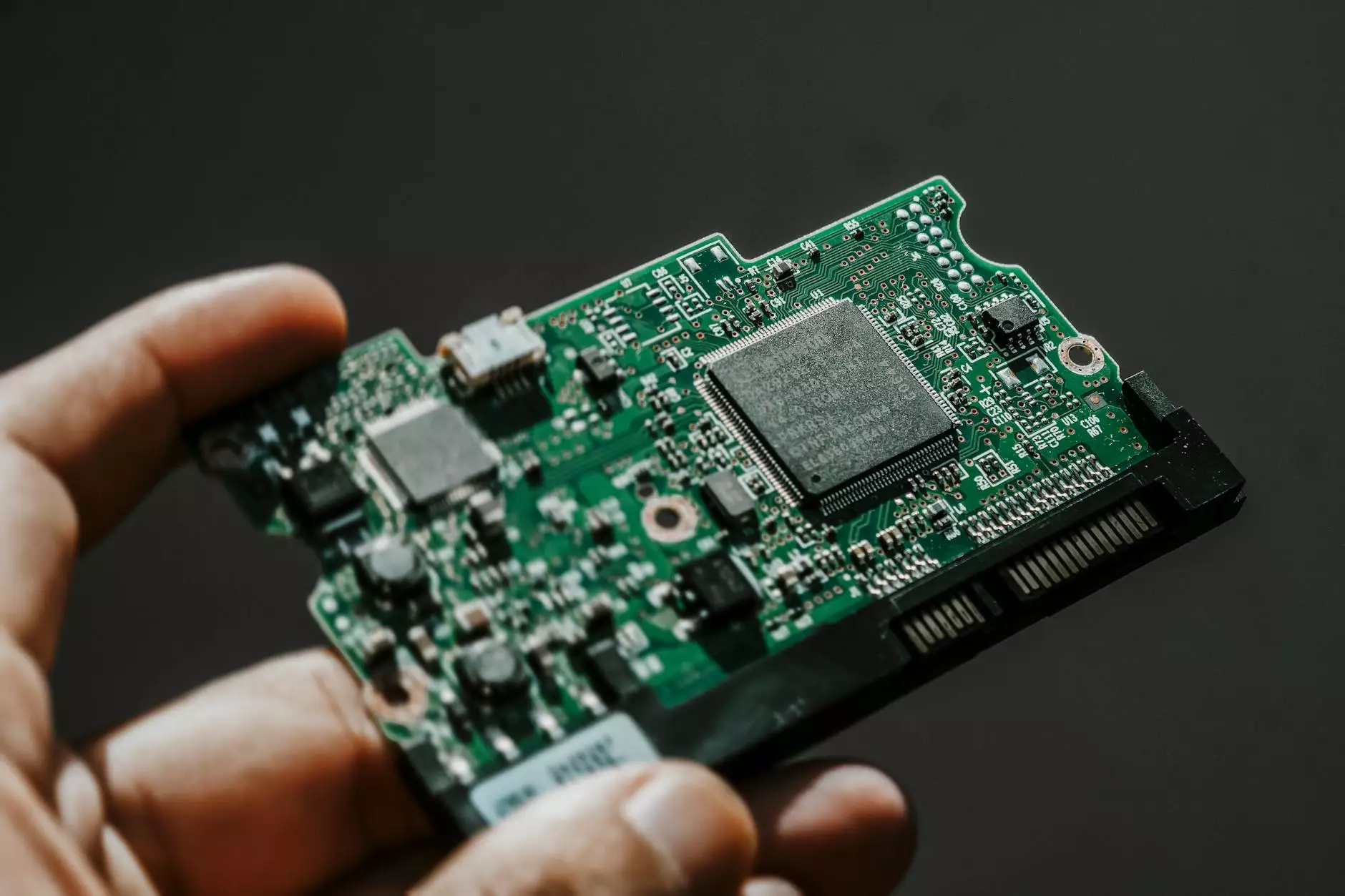
Tube connection types are fundamental components in various industries including manufacturing, plumbing, and construction. They provide a means to connect pipes, tubes, and sometimes hoses, ensuring that fluids can flow efficiently and safely. Selecting the right type of connection is crucial for the performance of any system. In this article, we will explore the different types of tube connections available, their benefits, and how they are used in practical applications.
What are Tube Connection Types?
Tube connection types refer to the specific styles and mechanisms used to join tubes and pipes together. Each type has unique characteristics, advantages, and ideal applications. Understanding these various types is essential for effective installation and maintenance in industrial applications.
Common Tube Connection Types
There are various categories of tube connections, each serving a particular purpose. Below are some of the most prominent tube connection types:
1. Tube Fittings
Tube fittings are devices that join two separate tubes or pipes. These fittings are critical in ensuring a leak-proof connection, optimizing flow, and maintaining pressure within the systems they operate in. Tube fittings come in various forms including:
- Compression fittings
- Flared fittings
- Quick disconnect fittings
Tube fittings are widely used in industries such as oil and gas, pharmaceuticals, and food processing.
2. Ferrule Fittings
Ferrule fittings are a specific type of tube fitting often used with tubing in high-pressure applications. The fitting consists of a ferrule (a small metal ring) that compresses around the tube to create a tight seal. Ferrule fittings are known for their reliability and are often found in:
- Hydraulic systems
- Pneumatic systems
- Chemical processing
These connections can withstand high temperature and pressure, making them ideal for demanding environments.
3. Forged Pipe Fittings
Forged pipe fittings are manufactured from a single piece of metal, providing superior strength and durability. These fittings are utilized in applications requiring high-pressure capabilities. Common types of forged fittings include:
- Elbows
- Tees
- Couplings
These sturdy connections are crucial in industries such as construction, maritime, and nuclear power.
4. Threaded Pipe Fittings
Threaded pipe fittings are designed to connect pipes using a series of threads that allow for a secure mechanical connection. These fittings are commonly used in systems where frequent disassembly and reassembly are necessary. Common examples include:
- Plumbing
- Oil and gas extraction
- Industrial water systems
Proper threading and sealing methods are vital to prevent leaks in these connections.
5. Flanges
Flanges are types of mechanical connectors that are used to connect pipes, valves, pumps, and other equipment to form a piping system. Flanges facilitate easy access to the piping system during maintenance; the most common types include:
- Weld neck flanges
- Blind flanges
- Slip-on flanges
Flanges are essential in oil and gas, chemical processing, and wastewater management applications.
Types of Valves in Tube Connections
In addition to fittings, various valves are essential in controlling fluid flow in tube systems. Here are crucial types of valves commonly used in conjunction with tube connections:
1. Check Valves
Check valves are designed to prevent backflow in a piping system. They ensure that the fluid flows in one direction, which is critical for protecting equipment and maintaining safety. Common uses of check valves can be found in:
- Pumping systems
- Heating systems
- Wastewater systems
The reliability of check valves makes them indispensable in many industrial applications.
2. Ball Valves
Ball valves are widely recognized for their durability and ability to provide a tight seal. They work by rotating a ball with a hole through the middle, controlling fluid flow when aligned or obstructed. Ball valves are commonly used in:
- Water and gas distribution systems
- Chemical manufacturing
- HVAC systems
The ease of operation and maintenance makes ball valves a preferred choice in many applications.
3. Needle Valves
Needle valves are particularly useful for regulating the flow of liquids and gases. Their design allows for fine adjustments, making them ideal for precise flow control. Needle valves are commonly used in:
- Laboratory applications
- Pneumatic systems
- Fuel control systems
The precision control offered by needle valves makes them a vital part of many engineering processes.
4. Manifold Valves
Manifold valves are used to connect multiple pipe or tube systems into a single entry point. They are especially important in applications requiring multiple connections to one source. Common applications include:
- Oil and gas extraction
- Power generation
- Manufacturing processes
Using manifold valves can optimize system efficiency and simplify maintenance processes.
Choosing the Right Tube Connection Type
Selecting the appropriate tube connection type involves considering several factors, including:
- Fluid Characteristics: Understand the nature of the fluid being transported (i.e., temperature, viscosity, corrosiveness). Some connections are better suited for specific fluids.
- Operating Pressure: Assess the pressure requirements of the system. High-pressure applications may necessitate stronger fittings or valves.
- Ease of Installation: Consider ease of installation and whether frequent maintenance will be necessary.
- Regulatory Standards: Ensure compliance with industry standards and regulations for safety and performance.
By taking these factors into account, businesses can ensure optimal performance and safety in their piping systems.
The Importance of Quality in Tube Connections
Ultimately, the quality of tube connection types can significantly impact the effectiveness of operations within any business. High-quality fittings and valves promote:
- Operational Efficiency: Reliable connections reduce the risk of leaks and failures, ensuring continuous operation of systems.
- Safety: Properly installed and maintained connections can prevent catastrophic failures, safeguarding both equipment and personnel.
- Cost Savings: Investing in quality decreases long-term maintenance costs and downtime, leading to better overall profitability.
Businesses like Tech Tubes provide a vast range of high-quality tube connection types that meet diverse industrial needs.
Conclusion
Understanding the various tube connection types is essential for anyone involved in industries that utilize fluid transport systems. By selecting the right fittings, valves, and connection types, businesses can ensure operational efficiency, safety, and long-term success. As industries evolve and technology progresses, staying informed about the advancements in tube connections will empower companies to make informed decisions for their infrastructure needs.
For more insights and quality supplies on tube fittings, ferrule fittings, forged pipe fittings, and more, visit Tech Tubes.